Höchst variabel
<p> Von ihrem Aussehen her lassen sich Elektroautos eher selten von herkömmlich angetriebenen Fahrzeugen unterscheiden. Wirft man hingegen einen Blick auf die Herzstücke des Elektroautos – den Motor und die Batterie – lassen sich sowohl hinsichtlich der Größe als auch der Anordnung der Komponenten wesentliche Unterschiede feststellen. Es fehlen sogar einige Bauteile, die in einem Fahrzeug mit Verbrennungsmotor zwingend benötigt werden. Stattdessen sind andere Bauteile gefragt. Daher ist es an der Zeit, dass Flottenmanagement einmal den Aufbau eines Elektrofahrzeugs sowie seiner Komponenten erklärt und dabei auf die Vor- und Nachteile eingeht.</p>
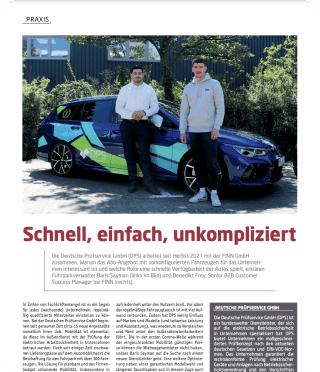
PDF Download
Essenziell, damit sich ein Elektrofahrzeug in Bewegung setzen kann, sind zwei Bestandteile: Das ist zum einen die Batterie als Energielieferant und zum anderen der Elektromotor, der das Antriebselement verkörpert. Bei der im täglichen Sprachgebrauch bezeichneten „Batterie“ eines Elektroautos handelt es sich im eigentlichen Sinne um einen Akkumulator (kurz: Akku), welcher einen wiederaufladbaren Energiespeicher darstellt. In der Praxis werden die Begriffe oft synonym verwendet. Der Akku eines Elektrofahrzeugs macht einen beträchtlichen Anteil des Gesamtfahrzeuggewichts aus: So setzt sich die maximale elektrische Reichweite, also die gespeicherte Energie in der Batterie, als Produkt aus Energiedichte (Wh/kg) und Masse der Batterie (kg) zusammen. Je größer die Energiedichte ist, desto mehr Energie kann bei gleichem Gewicht der Batterie gespeichert werden. Die derzeit oft verbauten Lithium-Ionen-Akkus weisen beispielsweise eine Energiedichte von circa 130 Wh/kg auf, im Vergleich zu einem Blei-Akku also eine vierfach höhere Energiedichte (30 Wh/kg). Die oft kritisch in der Öffentlichkeit diskutierte maximale elektrische Reichweite ist somit auch abhängig vom Gewicht des Lithium-Ionen-Akkus: So ergibt sich bei einem Gewicht von 230 Kilogramm eine maximale elektrische Reichweite der Batterie von 29,9 Kilowattstunden. Möchte man nun die tatsächliche Reichweite berechnen, muss nun auch der Verbrauch des Antriebselements in die Rechnung einbezogen werden. Die tatsächliche Reichweite ist dabei der Quotient aus maximaler elektrischer Reichweite geteilt durch den Verbrauch. Vereinfacht nehme man hier einen Verbrauch von 15 Kilowattstunden je 100 Kilometer an. Dadurch ergibt sich gerundet eine tatsächliche Reichweite von 200 Kilometern.
Aufbau eines Akkumulators
Der Akku eines Elektrofahrzeugs setzt sich in der Automobilindustrie aus mehreren Batteriezellmodulen zusammen, die wiederum aus einzelnen Batteriezellen bestehen. Durch diese Beschaffenheit kann der Akku skaliert und damit auch die Reichweite, wie zuvor beschrieben, an die jeweiligen Anforderungen angepasst werden. Eine Lithium-Ionen- Batteriezelle besteht aus der Anode (Kohlenstoff, Kupferfolie), einem Separator (poröse Polyolefin-Folie, keramikbeschichtet), einer Kathode (Lithium-Metall-Oxid, Aluminiumfolie) und einem Elektrolyt (organische Lösungsmittel, Lithium-Leitsalz, Additive). Beim Laden wandern die Lithium-Ionen von der Kathode zur Anode und werden dort gespeichert. Die elektrische Energie – eingespeist aus dem Stromnetz über das Ladekabel – wird dabei in chemische Energie umgewandelt. Beim Entladevorgang – zum Betrieb des Elektromotors – wandern die Lithium-Ionen zurück zur Kathode. Die chemische Energie wird dabei wieder in elektrische Energie umgewandelt. Grundsätzlich werden für die Herstellung von Lithium- Ionen-Batteriezellen für Elektroautos fünf Hauptrohstoffe benötigt. Auf der Kathodenseite fungiert eine Verbindung der Elemente Kobalt, Nickel und Mangan durch ihre Struktur als Speicherort für die Speicherung des Ladungsträgers Lithium, auf der Anodenseite ist dies Grafit. Des Weiteren ist Lithium im Elektrolyt enthalten. Lithium gilt dabei als derzeit konkurrenzloser, auf absehbare Zeit unersetzlicher Ladungsträger, da kein anderes Element vergleichbare Eigenschaften für automobile Batterieanwendungen bietet.
Innerhalb des Modularen E-Antriebs-Baukastens (kurz: MEB) von Volkswagen ist der Lithium-Ionen-Akku in ein Aluminium-Batteriegehäuse mit Crashrahmen eingebettet: Die unterste Ebene bildet ein solider Auffahrschutz. Darüber angeordnet ist das Aluminium-Batteriegehäuse mit einem Crashrahmen, der integrierten Batteriekühlung und einer Anschlussbox für das Hochvolt- und Niedervolt-Bordnetz (AC, DC und 12 V). In das Batteriegehäuse eingesetzt werden die neu entwickelten modularen Lithium-Ionen-Batterien. Die Zell-Controller (CMCe) – Steuergeräte für die Überwachung der Zellen (Spannung, Ströme und Temperatur) und das Zell-Balancing (Sicherstellen gleicher Belastung der Zellen im täglichen Betrieb) – sind im Gehäuselängsträger der Batterie eingebaut. Im hinteren Teil des Batteriesystems ist als weiteres Steuergerät die Batterieelektronik (BMCe) integriert. Über sogenannte Zellmodulverbinder werden die Zellmodule miteinander vernetzt; Messleitungen kommunizieren indes mit der Batterieelektronik. Geschlossen wird das Batteriegehäuse nach oben hin mit einem Deckel, der zur eventuellen Wartung einfach entfernt werden kann.
Ein bis vier Antriebselemente
Die im Lithium-Ionen-Akku gespeicherte Energie fließt über die Leistungselektronik zu den Antriebselementen. Im Gegensatz zum Aufbau eines Fahrzeugs mit Verbrennungsmotor können durch das Fehlen einiger Teile des konventionellen Antriebsstrangs – Schwungrad, Kupplung und Schaltgetriebe – beliebig viele Antriebselemente angeschlossen werden. Theoretisch sind auch Antriebswellen und das Differential nicht mehr nötig, dafür müssten die Elektromotoren jedoch direkt die Räder antreiben und der Elektromotor müsste nicht wie oft auf die angetriebene Achse gesetzt werden. Die zuvor angesprochene Leistungselektronik wandelt den in der Batterie gespeicherten Gleichstrom (DC) in Wechselstrom (AC) um. Über einen DC-DC-Wandler wird indes die Bordelektronik mit 12 Volt versorgt. Die Kraftübertragung vom Motor an die Hinterachse erfolgt über ein Ein-Gang-Getriebe. Motor, Leistungselektronik und Getriebe bilden dabei eine kompakte Einheit.
Grundsätzlich teilen sich die Motoren elektrisch angetriebener Fahrzeuge in zwei Kategorien auf: Gleichstrommotoren und Wechselstrommotoren. Ihre Bezeichnung haben Gleichstrommotoren aufgrund des Stromflusses erhalten. Dieser bewegt sich konstant in eine Richtung. Der Motorentyp ist durch ein vergleichsweise hohes Gewicht und große Abmessungen gekennzeichnet. Aufgrund dieser Eigenschaften eignen sich Motoren dieses Typs nicht für moderne Elektrofahrzeuge, da einerseits das Gesamtgewicht des Fahrzeugs steigen würde und andererseits die Fahrzeuge weniger kompakt konzipiert werden könnten. Daher werden ausschließlich Wechselstrommotoren als Antriebselemente in E-Autos genutzt: Wie die Bezeichnung zu erkennen gibt, besteht bei diesen Maschinen die Möglichkeit, die Richtung des Stromflusses zu ändern. Die Folge ist, dass sich verschiedene Spannungen ideal umwandeln lassen. Wechselstrommotoren können zudem extrem hohe Drehzahlen bis zu 20.000 Umdrehungen erreichen. Bei den Wechselstrommotoren differenziert man zudem zwischen Asynchronmotoren und Synchronmotoren.
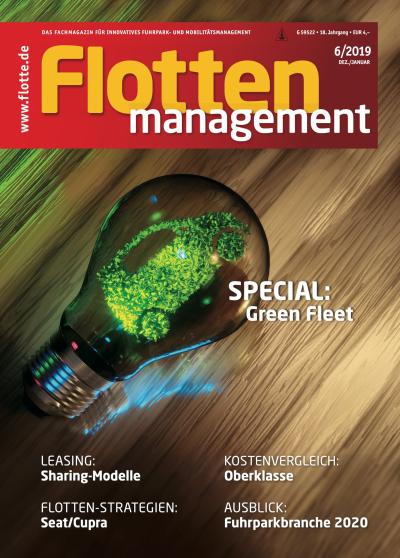
Aktuelles Magazin
Ausgabe 6/2019

Sonderausgabe Elektro
Das neue Jahresspecial Elektromobilität.
Die Bezeichnung der Asynchronmotoren ist auf die Erzeugung des Magnetfelds zwischen dem Rotor und den Statoren zurückzuführen. Sie verläuft mit einer gewissen Zeitverzögerung, weswegen sie als asynchron beschrieben wird. Dieser Motortyp ist durch einen recht simplen Aufbau gekennzeichnet. Der Rotor setzt sich lediglich aus einem Blechpaket sowie einer Kurzschlusswicklung zusammen. Der geringe Verschleiß ist ein Vorteil für den Einsatz von Asynchronmotoren. Außerdem erreicht dieser Motorentyp hohe Drehzahlen. Nicht unerwähnt soll bleiben, dass der Einsatz sogenannter Seltener Erden nicht vonnöten ist. Als Seltene Erden werden teure und rar vorkommende Industriemetalle bezeichnet, zu denen etwa Dysprosium oder Neodym gehören. Diese kommen als Bestandteile in Magneten vor. Dennoch sind Asynchronmotoren für E-Autos nur noch bedingt relevant. Dies liegt vor allem daran, dass Synchronmotoren eine noch höhere Leistungsdichte und einen optimaleren Wirkungsgrad bieten. So sind sie in der Lage, möglichst viel der zugeführten elektrischen Energie in tatsächliche, mechanische Energie umzuwandeln. Bei diesen Maschinen bewegt sich der Rotor synchron zum magnetischen Drehfeld – daher entstammt die Bezeichnung. Beinahe alle Hersteller von E-Autos greifen mittlerweile auf Synchronmotoren zurück.
Erst Ende Juni hatte die BMW Group im Rahmen der #NEXTGen den Versuchsträger „Power BEV“ gezeigt, der das technisch Machbare auslotet. Als Basis diente ein aktuelles Serien-Fahrzeug der BMW 5er-Reihe. Der Versuchsträger verfügt jedoch über drei Elektromotoren der fünften E-Antriebsgeneration, bei denen jeweils eine E-Maschine mit der dazugehörigen Leistungselektronik und dem Antrieb in einem gemeinsamen Gehäuse untergebracht sind. Eine ist an der Vorderachse eingebaut, zwei an der Hinterachse – ausgeführt als Doppel-Antriebseinheit. Neben der Leistung ist bei dieser Generation bemerkenswert, dass sie völlig ohne Seltene Erden auskommt. Gleichermaßen blieb durch die Integration eines solchen Antriebssystems der gesamte Fahrgastraum vollständig ohne Einschränkungen erhalten. Dies erleichtert deutlich die Beurteilung des Antriebskonzepts im Vergleich mit anderen. Die Ingenieure konnten so auch noch besser analysieren, welche Möglichkeiten zwei getrennt ansteuerbare E-Maschinen an der Hinterachse mit E-Torque-Vectoring eröffnen. Erstmals in Serie geht eine solche E-Maschine mit dem BMW iX3 – wohlgemerkt eine pro Fahrzeug.
Viele Möglichkeiten für die Karosserie
Neben den essenziellen Bestandteilen eines Elektrofahrzeugs ist auch der Karosserie ein hohes Maß an Aufmerksamkeit zu schenken. Ohnehin spielt sie bei allen Arten von Fahrzeugen eine wichtige Rolle, wenn es darum geht, die Insassen und alle im Inneren verbauten Komponenten bestmöglich zu schützen. Andererseits trägt sie als Formgeber zur Optik und Ästhetik des Fahrzeugs bei, um einen hohen Wiedererkennungswert zu schaffen und eine Differenzierung gegenüber anderen Modellen zu bieten. Insbesondere in den vergangenen Monaten ist ein sichtlicher Sprung im Design der E-Autos gelungen. So überzeugten viele der ersten E-Autos die Autoliebhaber auch aufgrund des äußeren Erscheinungsbildes nicht. Mittlerweile gibt es von kompakt über sportlich bis luxuriös alle Designvariationen, auch SUV-Modelle sind keine Seltenheit.
Beim Design unterscheidet man grundsätzlich nach Conversion und Purpose Design. Der englische Begriff „conversion“ bedeutet ins Deutsche übersetzt so viel wie eine Umwandlung oder auch einen Umbau. Übertragen auf die Karosserie eines elektrisch angetriebenen Pkws, zielt diese Idee darauf ab, dass schlichtweg das Design eines bereits vorhandenen Fahrzeugs mit Verbrennungsmotor herangezogen wird. Das ursprüngliche Modell verwandelt sich dann gewissermaßen in ein E-Auto, indem es nur zu einer Anpassung der für den Betrieb erforderlichen Bauteile kommt. Für den Hersteller selbst ist dieses Prinzip sinnvoll und kostenoptimierend. Der Aufwand und der Kostenfaktor für eine Neuentwicklung wären wesentlich höher. Auch entstehen bei Reparaturen an der Karosserie weniger Probleme, da die Blaupausen und Ersatzteile adaptiert werden können. Somit ändert sich das Handling in den Werkstätten für die ausführenden Mechaniker nicht sonderlich.
Im Mercedes-Benz EQC finden sich viele Elemente eines Conversion Designs: So erinnern die Proportionen und die gestreckte Dachlinie an den GLC. Die sportliche, langgezogene Silhouette schließt am Heck mit einem tief heruntergezogenen Dachspoiler ab. Dachkontur und Seitenscheibengrafik signalisieren optisch die Zugehörigkeit zum Segment der Crossover-SUV. Der Innenraum wirkt bekannt, viele Bedienelemente sind an bekannter Stelle – auch eine Mittelkonsole, die sich zwischen beiden Sitzen bis in den Fond zieht, ist mit an Bord. Damit zeigt sich auch ein Nachteil am Conversion Design: Da die Grundkonzeption des E-Autos stark an der für Fahrzeuge mit Verbrennungsmotor orientiert ist, kann das volle Potenzial, das durch die Möglichkeit, Elektromotoren und Akkus zu platzieren, gegeben ist, nicht vollends ausgeschöpft werden. Es ist somit ein kompromissbereites Verschmelzen von Alt und Neu. Dementgegen zielt das Purpose Design darauf ab, das Fahrzeug komplett optimiert für die Elektromobilität zu kreieren. Es ist das konsequente Konzipieren eines E-Autos, ohne Kompromisse mit den Gegebenheiten aus der Verbrenner- Technologie eingehen zu müssen. Insbesondere in Konzeptfahrzeugen für das autonome Fahren ist das Purpose Design zu finden, um ein hohes Maß an Flexibilität des Innenraumes zu erzielen. Jedoch birgt dieses Design für Hersteller ein höheres Risiko: Nicht nur die Investitionen für ein komplett neues Concept-Car inklusive der dafür benötigten Zeit und Ressourcen sind aufwendig, sondern auch der komplette Herstellungsprozess bis hin zum Teileeinkauf bei Zulieferern muss neu entstehen.
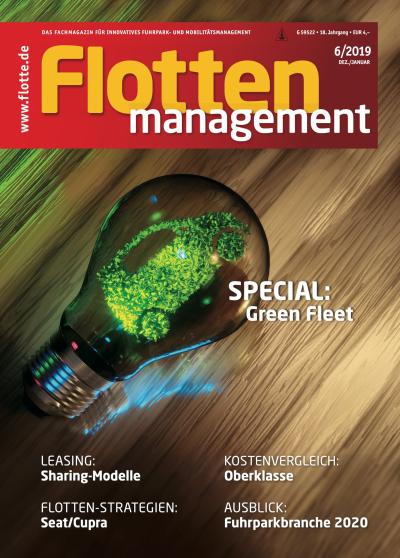
Aktuelles Magazin
Ausgabe 6/2019

Sonderausgabe Elektro
Das neue Jahresspecial Elektromobilität.
Der nächste „Flotte!
Der Branchentreff" 2026
0 Kommentare
Zeichenbegrenzung: 0/2000